Thursday, November 21, 2024
How to Make a Lean-To Shed DIY: A Low-Cost Outdoor Project

How to Make a Lean-To Shed DIY: A Low-Cost Outdoor Project
Dreaming of extra storage space without breaking the bank? A lean-to shed is the perfect solution! This simple, DIY project offers a surprisingly spacious addition to your yard, perfect for storing gardening tools, bicycles, or even firewood. This guide walks you through the entire process, from planning and material gathering to construction and finishing touches. Get ready to build your own affordable and practical lean-to shed!
Planning Your Lean-To Shed
Before you even think about grabbing a hammer, careful planning is key. Start by determining the size and location of your future shed. Consider the available space against your house or fence, the amount of storage you need, and any local building codes or restrictions. Sketch a simple design, noting dimensions and material requirements. A smaller lean-to is easier and cheaper to build, but make sure it's big enough for its intended purpose. Also, think about the orientation; you'll want to position it to minimize exposure to harsh weather elements.
Choosing Your Materials
Selecting the right materials is crucial for both the structural integrity and the overall cost of your project. Pressure-treated lumber is highly recommended for the frame, as it's resistant to rot and insects. For the roof, consider using inexpensive materials like corrugated metal sheeting or even heavy-duty plastic sheeting. You can also recycle some materialsâ"old pallets can provide useful lumber for less critical parts of the structure. Remember to account for screws, nails, and any additional hardware you might need.
Building the Frame
With your materials gathered, begin constructing the frame. This involves creating a sturdy base that will support the roof. Start by attaching the vertical supports to your existing structure (house or fence). Ensure they are plumb and securely fastened using appropriate screws or bolts. Next, attach the horizontal supports to create the framework of your shed. Remember to measure twice and cut once to maintain accuracy and prevent costly mistakes. A level will be your best friend during this stage.
Step-by-Step Frame Construction
- Securely attach the vertical support posts to your existing structure.
- Measure and cut the horizontal support beams.
- Attach the horizontal beams to the vertical supports, ensuring they are level and square.
- Check for stability and adjust as needed.
Installing the Roof
Once the frame is complete, it's time to install the roof. If using corrugated metal sheeting, carefully measure and cut the sheets to fit your frame. Overlap the sheets appropriately to ensure watertightness. Secure the sheets with appropriate fasteners, ensuring they are firmly attached to the frame. If using plastic sheeting, stretch it taut and secure it with battens and screws. Consider adding a slight slope to the roof to facilitate water runoff.
Adding the Finishing Touches
While the basic structure is now complete, adding finishing touches will enhance both the aesthetics and functionality of your lean-to. Consider adding a simple door if desired, using readily available materials or even repurposing an old door. You may want to paint the wood for added protection from the elements and to improve the shed's appearance. Think about adding some shelves or hooks to maximize storage space inside.
Safety First!
Safety should always be your top priority. Wear appropriate safety gear, including safety glasses and work gloves. Use caution when working with power tools and sharp objects. Ensure the structure is stable and securely anchored before storing any items inside.
Building your own lean-to shed is a rewarding experience that combines practicality and cost-effectiveness. By following these steps, you can create a valuable addition to your property for minimal expense. So, gather your tools, get creative, and enjoy the satisfaction of completing your very own DIY project!
How to Build a Basic Shed with Simple, Cost-Effective Plans
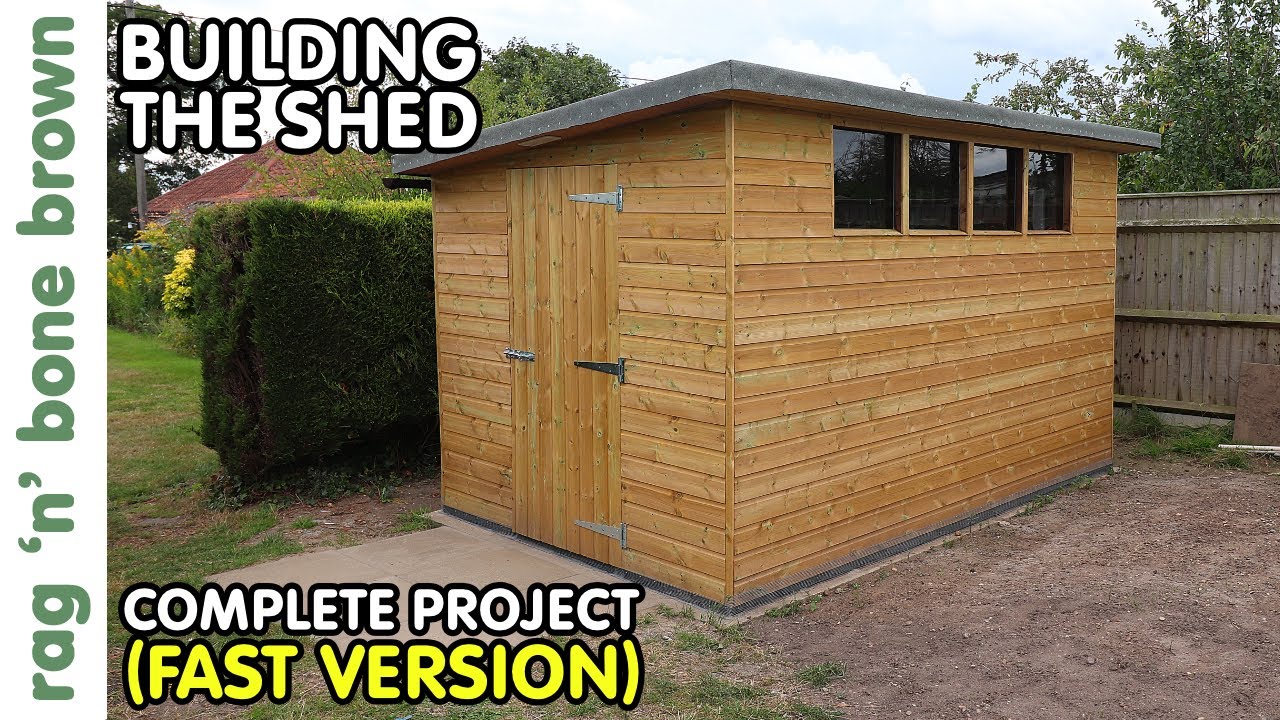
Building Your Dream Shed: A Simple, Budget-Friendly Guide
Hey there, folks! So you're dreaming of a shed, huh? Maybe a place to store your gardening tools, a workshop for your hobbies, or just a little extra storage space. Building a shed yourself can seem daunting, but trust me, it's totally doable, even on a budget! This guide will walk you through building a basic shed with simple plans that won't break the bank. Letâs get started!Planning Your Perfect Shed
Before you even think about grabbing a hammer, you need a plan. This isn't about complicated blueprints; we're keeping it simple!Size and Location
First things first: how big do you need your shed to be? Think about what you'll be storing. A 6' x 8' shed is a good starting point for most people, providing plenty of space without being overly ambitious for a first-time builder. Bigger is always more expensive and complex! Remember to check your local building codes regarding shed size and placement. You'll also need to consider access â" ensure you have enough room to get materials to the location and that it's not going to block any walkways or utilities.
Materials List: Keeping it Budget-Friendly
This is where you can really save money. Don't go for the most expensive lumber; pressure-treated lumber is a good, affordable choice. You'll need:
- Pressure-treated 4x4 posts for the foundation
- Pressure-treated 2x4s for the frame
- Plywood for the walls and roof
- Roofing material (shingles, metal, etc.) â" consider affordability and longevity
- Screws and nails (galvanized for outdoor use)
- Door hardware
- Optional: Window(s)
- Concrete for the foundation (optional; you could use gravel or even a wooden base, but concrete is most durable)
Shop around! Check local lumber yards, home improvement stores, and even consider reclaimed materials if youâre feeling adventurous (and environmentally conscious!).
Building the Foundation: A Solid Start
A strong foundation is crucial. While concrete is ideal, it adds cost and complexity. A simpler option, especially if the ground is fairly level, is a gravel base. Here's how to do both:
Concrete Foundation
Dig out your foundation area to a depth of about 6 inches. Place your 4x4 posts in the holes and level them carefully. Pour concrete around the posts, making sure they remain plumb (perfectly vertical) and level. Let it cure completely according to the concrete's instructions (usually 24-48 hours).
Gravel Base Foundation
Level the ground where your shed will sit. Lay down a layer of landscape fabric to prevent weeds. Next, add a layer of compacted gravel (around 4-6 inches). This will provide drainage and a relatively level base for your shed. Make sure your 4x4 posts are level on this compacted gravel.
Framing the Shed: The Skeleton
Now for the fun part! This is where you build the frame of your shed, using your 2x4s. You'll need to create the floor frame first, then the walls, and finally the roof frame.
Floor Framing
Build a rectangular frame on top of your foundation, using 2x4s. This will be the base for your plywood floor. Attach the floor joists (2x4s running across the frame) every 16 inches, ensuring they're level and evenly spaced.
Wall Framing
Construct the walls separately. You'll need to cut 2x4s to the correct height, creating a frame for each wall. Once again, ensuring everything is perfectly square and level. Attach the plywood sheathing to the frames.
Roof Framing
The simplest roof is a gable roof (two sloped sides). You'll need to build two triangular frames that meet at the top, creating a ridge. Attach these frames to the top of the walls, carefully ensuring they're perfectly aligned.
Sheathing and Roofing: Finishing Touches
Once the frame is complete, itâs time to cover it up!
Sheathing
Attach plywood sheathing to the walls and floor. This will create a solid surface and protect the frame from the elements. Use appropriate screws to secure the plywood.
Roofing
This is where your choice of roofing material comes into play. Shingles are relatively easy to install, while metal roofing is more durable but can be trickier for beginners. Follow the manufacturer's instructions carefully for your chosen material. Remember proper ventilation is key â" consider adding vents to your roof to prevent moisture buildup.
Adding the Finishing Touches: Doors, Windows, and More!
The final steps involve installing the door, any windows you've chosen, and adding any trim work you like. Follow the instructions provided with your door and window hardware. You might consider adding a little paint or stain to protect the wood and add some curb appeal.
Safety First!
Throughout the entire building process, always prioritize safety. Wear safety glasses and work gloves. Use caution when handling power tools, and be sure to take breaks when you need them. If you're unsure about any step, donât hesitate to seek help from a more experienced builder or consult online resources.
Commonly Asked Questions
Q: How long does it take to build a shed?
A: This varies greatly depending on your experience and the complexity of your design. A basic shed like this could take a weekend for an experienced builder or a few weekends for a beginner.
Q: Do I need a permit to build a shed?
A: Building codes vary by location. Check with your local authorities before you start. Smaller sheds may not require a permit, but it's always best to be sure.
Q: Can I build this shed by myself?
A: While it's possible, having a helper can make the process much easier, especially for lifting and positioning heavy materials.
Q: What kind of tools do I need?
A: You'll need basic hand tools (hammer, measuring tape, level, saw), plus power tools are helpful (drill, circular saw). A post-hole digger will be essential if using a concrete base.
Q: How much will this cost?
A: The cost depends heavily on material choices and your location. However, you should be able to build a basic shed for under $1000, depending on where you live and what kind of materials you choose.
Remember, building a shed is a rewarding project. Take your time, be patient, and enjoy the process! Good luck, and happy building!
Step-by-Step Lean-To Shed Build: Create a Shed for Your Backyard

A Comprehensive Guide to Lean-To Shed Construction
This document provides a detailed, step-by-step guide for constructing a lean-to shed. Lean-to sheds, characterized by their single sloped roof design, are a versatile and relatively straightforward shed type, ideal for beginners and experienced DIY enthusiasts alike. Careful planning and meticulous execution are paramount to ensuring a structurally sound and aesthetically pleasing finished product. This guide will cover all aspects of the build, from initial design and material selection to final finishing touches.
Phase 1: Planning and Design
The initial phase focuses on meticulous planning, which significantly impacts the projectâs success. This involves determining the shed's dimensions, location, and material specifications. Careful consideration at this stage prevents costly mistakes and ensures the shed meets your specific requirements.
1.1 Determining Shed Dimensions and Location
The first step is to decide on the dimensions of your lean-to shed. Consider the intended use; a shed for storing gardening tools requires less space than one intended for housing larger equipment. Common dimensions range from 6ft x 8ft to 10ft x 12ft, but this can be adjusted based on your needs and available space. The location should be carefully chosen, considering factors such as sunlight exposure, proximity to utilities, and accessibility. Ensure compliance with local building codes and regulations regarding setbacks from property lines.
1.2 Material Selection
Material selection directly impacts the shedâs durability, aesthetics, and cost. Common choices include pressure-treated lumber for its resistance to rot and insect damage, and plywood for sheathing. Consider using galvanized steel for roofing to ensure longevity and weather resistance. Always purchase materials from reputable suppliers to guarantee quality and consistency. A detailed materials list should be compiled, including quantities, ensuring you have enough materials to avoid delays during construction.
1.3 Obtaining Necessary Permits
Before commencing construction, check with your local building department to determine if a permit is required. This step is crucial, as building without a permit can result in fines or even demolition orders. The permit application process might require submission of detailed plans and specifications, so itâs crucial to have well-defined plans before applying.
Phase 2: Foundation and Framing
This phase involves constructing a solid foundation and erecting the frame, the skeletal structure upon which the shed's walls and roof will be built. A stable foundation is essential for the long-term stability of the entire structure.
2.1 Foundation Construction
A simple concrete slab is a suitable foundation for a lean-to shed. Alternatively, a compacted gravel base can be used for less demanding structures. The foundation's dimensions should match the shed's footprint, providing a level and stable platform. If using a concrete slab, ensure proper curing time before proceeding to the next stage. For a gravel base, ensure thorough compaction to prevent settling.
2.2 Framing the Walls and Roof
The framing involves constructing a sturdy framework using pressure-treated lumber. The wall frame consists of vertical studs attached to a base plate and top plate. The roof framing involves constructing rafters that slope from a higher point (attached to the existing structure) to a lower point (resting on the wall frame). Ensure accurate measurements and proper connections using appropriate fasteners, including nails and screws. The use of a level and plumb bob is crucial for ensuring accurate framing. Appropriate bracing should be incorporated to maintain structural integrity.
Phase 3: Sheathing and Roofing
Once the framing is complete, the next step involves applying sheathing to the walls and installing the roofing material. This provides weather protection and a surface for finishing materials.
3.1 Wall Sheathing
Plywood or OSB (Oriented Strand Board) is commonly used for wall sheathing. Secure the sheathing to the wall frame using appropriate nails, ensuring proper spacing and overlap. Proper sealing of all joints is crucial to prevent water penetration. Consider using housewrap as an additional layer for enhanced weather protection.
3.2 Roof Sheathing
Similar to wall sheathing, roof sheathing provides a solid surface for the roofing material. Ensure proper overlap and secure fastening to the rafters. A layer of underlayment should be applied over the sheathing to act as a water barrier before installing the roofing material.
3.3 Roofing Installation
Galvanized steel roofing is a popular choice for its durability and weather resistance. Install the roofing material according to the manufacturerâs instructions, ensuring proper overlap and secure fastening. Pay close attention to the flashing around the edges and any penetrations to prevent leaks.
Phase 4: Finishing Touches
This final phase involves adding the finishing touches to complete the shed. This includes installing doors, windows, and any other desired features.
4.1 Door and Window Installation
Install pre-hung doors and windows according to the manufacturer's instructions. Ensure proper sealing and weatherstripping to prevent drafts and water infiltration. The use of shims is crucial to ensure proper alignment and level installation. Secure the doors and windows to the framing using appropriate fasteners.
4.2 Exterior Finishing
Once the doors and windows are installed, consider applying an exterior finish such as paint or stain to protect the wood from the elements and enhance aesthetics. Select a weather-resistant product suitable for exterior use. Allow ample drying time between coats.
4.3 Interior Finishing (Optional)
Consider adding interior features such as shelving, workbenches, or electrical wiring depending on the intended use of the shed. If installing electrical wiring, ensure compliance with all relevant electrical codes and regulations. It's advisable to consult with a qualified electrician for this task.
Phase 5: Final Inspection and Cleanup
Conduct a thorough inspection of the completed shed to verify that all aspects meet your requirements and local building codes. Address any defects or deficiencies before declaring the project complete. Finally, clean up the construction site, removing all debris and waste materials responsibly.
Disclaimer: This guide provides general information and should not be considered a substitute for professional advice. Always adhere to local building codes and regulations. If you are unsure about any aspect of this project, consult a qualified professional.
Functional Basic Shed Plans for Storing Tools and Equipment

Building Your Dream Basic Shed: A Simple Guide to Functional Tool Storage
So, you're thinking about building a shed? Fantastic! Whether you're a seasoned DIYer or just starting out, building a shed is a rewarding project that can dramatically improve your home's organization and functionality. This guide will walk you through creating a basic, functional shed perfect for storing your tools and equipment. We'll keep it simple, focusing on practicality and ease of construction, even for beginners.
Planning Your Shed: Size, Location, and Materials
Before you even think about grabbing a hammer, let's plan this out. The first step is deciding on the size. How much stuff do you need to store? Think about lawnmowers, garden tools, bikes, maybe even some lumber. A good starting point for a basic shed is around 8ft x 6ft. This provides ample space without being overwhelming for a first-time builder. Consider adding a foot or two in either dimension if you anticipate needing more space in the future. Itâs always better to have a little extra room than to wish you had it!
Choosing the Perfect Location
Where you place your shed is crucial. You want it easily accessible, but also consider things like:
- Sunlight: Too much direct sunlight can damage stored items. Try to find a spot with some shade.
- Drainage: Ensure the ground drains well to prevent water accumulation around the shed's foundation.
- Access: Make sure you have easy access for transporting materials during construction and for accessing the shed afterward. Consider the proximity to power outlets if you plan on using electricity inside.
- Local Regulations: Check with your local council or homeowner's association for any building regulations or restrictions regarding shed placement. This is important to avoid future complications!
Selecting Your Building Materials
Choosing the right materials will heavily influence the look, durability, and cost of your shed. Here's a breakdown of common choices:
- Pressure-treated lumber: This is a popular choice for the framing due to its resistance to rot and insects. It's slightly more expensive but worth the investment for longevity.
- Plywood or OSB (Oriented Strand Board): These are common choices for the siding and roofing. Plywood tends to be slightly more expensive but offers a smoother finish. OSB is a more affordable alternative but can be less visually appealing.
- Roofing felt and asphalt shingles: These provide good weather protection for your shed. Make sure you pick a shingle that's right for your climate.
- Concrete blocks or a simple slab: A concrete base is ideal for stability and moisture protection. If building on less stable ground, consider using concrete piers for support.
Basic Shed Construction: A Step-by-Step Guide
Now for the fun part! This is a simplified overview â" more detailed plans are readily available online. Always prioritize safety and follow proper construction techniques.
Step 1: Preparing the Foundation
Start by levelling the ground and creating a solid foundation. This could be a concrete slab, a gravel base, or concrete blocks set in the ground. The foundation should be slightly larger than the shed's footprint to ensure stability.
Step 2: Framing the Floor
Once the foundation is set, you can build the floor frame using pressure-treated lumber. This involves creating a grid of beams and joists to support the plywood or OSB flooring. Make sure your joists are spaced appropriately to avoid sagging.
Step 3: Erecting the Walls
Assemble the wall frames using pressure-treated lumber, ensuring they are square and plumb. Use proper bracing to maintain stability during construction. Once the walls are assembled, attach the plywood or OSB sheeting.
Step 4: Building the Roof
Construct the roof frame, which will likely be a simple gable or shed roof. Remember to factor in the appropriate overhang to protect the walls from rain. Once the frame is complete, cover it with roofing felt and asphalt shingles.
Step 5: Adding the Door and Windows
This is where your shed starts to take shape! Install a sturdy door thatâs appropriately sized for your needs, and consider adding windows for light and ventilation. Make sure youâve got robust hinges and a secure locking mechanism.
Step 6: Finishing Touches
Finally, add any finishing touches, such as painting or staining the exterior, adding shelves or workbenches inside, and installing any necessary hardware.
Tips for Success
- Start with detailed plans: Even for a basic shed, having detailed plans will save you time and headaches.
- Use quality materials: Investing in good materials will result in a more durable and long-lasting shed.
- Take your time: Rushing the process can lead to mistakes. Focus on accuracy and precision.
- Ask for help: Donât hesitate to ask for help from friends or family, especially for lifting heavier components.
- Check your work regularly: Ensure everything is square and plumb throughout the building process.
Commonly Asked Questions
Here are some frequently asked questions about building a basic shed:
Q: Do I need a building permit?
A: This depends on your local regulations. Check with your local council or homeowner's association before you begin construction to avoid any potential issues.
Q: How long does it take to build a shed?
A: The time required varies depending on your experience and the complexity of the design. A basic shed can typically be built in a weekend or two, while more complex designs may take longer.
Q: How much does it cost to build a shed?
A: The cost varies greatly depending on the size, materials, and features. You can expect to spend anywhere from a few hundred to a couple of thousand dollars.
Q: Can I add electricity to my shed?
A: Yes, but you'll need to consult with a qualified electrician to ensure it's done safely and according to code.
Q: What about insulation?
A: Insulation is a great idea if you plan on using the shed year-round. Adding insulation will help regulate the temperature and create a more comfortable space.
Building a shed is a rewarding experience. By following these simple steps and taking your time, you can create a functional and attractive storage solution for years to come. Happy building!
DIY Lean-To Shed Build: Low-Cost Plans for a Functional Shed
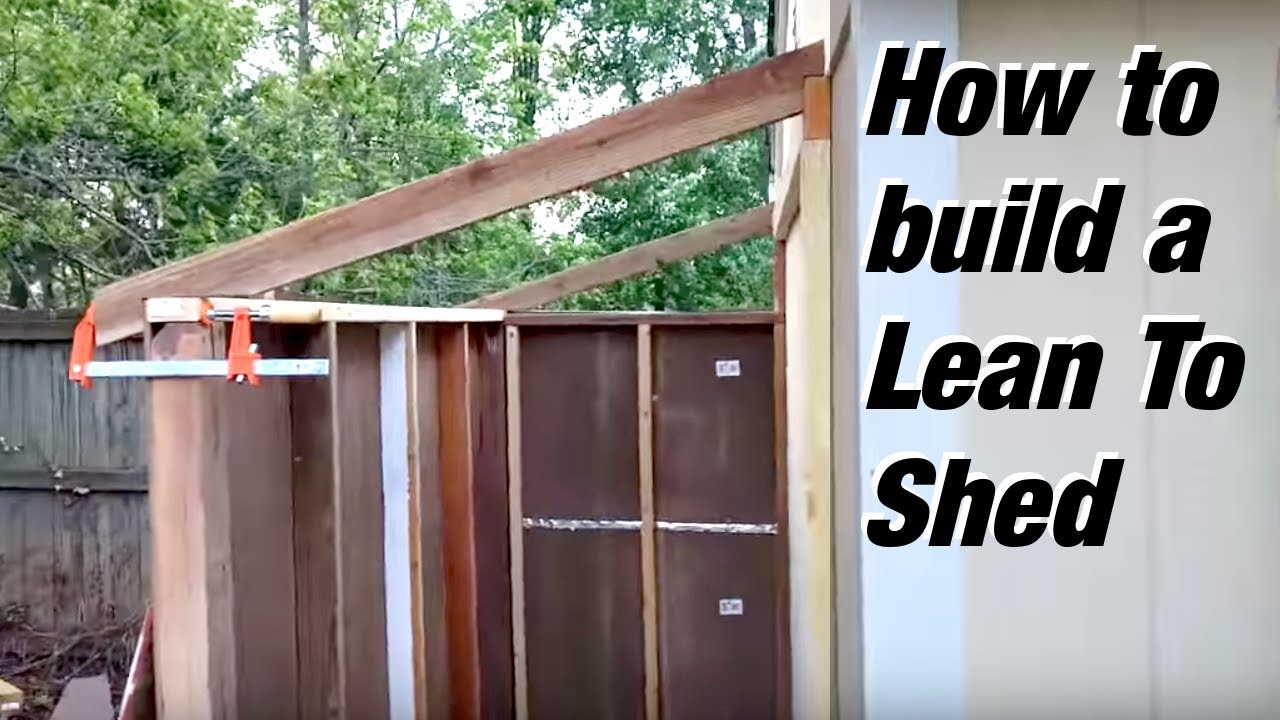
DIY Lean-To Shed Build: Low-Cost Plans for a Functional Shed
So, you're dreaming of a shed, huh? That extra space for your tools, gardening supplies, or maybe even a cozy little workshop. But the cost of pre-built sheds can be, let's just say, a bit steep. Fear not, fellow DIY enthusiast! Building your own lean-to shed is totally achievable, even on a budget. This guide walks you through the process, offering practical tips and tricks to keep costs down without sacrificing functionality.
Planning Your Lean-To Shed: Dreaming Big (But Starting Small)
Before you grab a hammer, let's get organized. Planning is crucial, especially for a budget-friendly build. Think about what you need this shed for. A simple storage space requires less elaborate construction than a workshop. This will dictate size, materials, and features.
Choosing the Right Spot:
Location, location, location! Consider these factors:
- Accessibility: Will you need easy access with a vehicle to unload materials?
- Sunlight & Shade: Do you want a sunny spot for drying things or a shady spot to protect items from the sun?
- Drainage: Ensure the area has good drainage to prevent water buildup and rot.
- Existing Structures: Lean-tos are perfect for attaching to existing buildings like garages or houses. This can save on materials (for one wall!)
Determining the Size:
Measure carefully! Start with the essential items you'll be storing to determine the minimum space required. Remember to leave enough room to move around comfortably inside.
Budgeting and Material Selection:
This is where you get to be really savvy. Scour local salvage yards, Craigslist, and Facebook Marketplace for reclaimed lumber. You'd be surprised what treasures you can find at a fraction of the cost of new materials. Consider using readily available and affordable materials like pressure-treated lumber for the base and framing.
Gathering Your Tools and Materials:
Now for the fun part (almost!). Here's a list of essential tools and materials you'll need. Again, remember that you can often find used tools in good condition at a significant discount. Borrowing tools from friends or family is another great budget-friendly option!
Essential Tools:
- Measuring tape
- Level
- Shovel
- Post hole digger (or a strong friend!)
- Hammer
- Saw (circular saw is ideal, but a hand saw works too)
- Drill with various drill bits
- Screwdriver (or drill with screwdriver bits)
- Safety glasses and gloves
Essential Materials (Quantities depend on your shed size):
- Pressure-treated lumber for the base and framing
- Plywood or other sheeting for the walls and roof
- Roofing felt or other roofing material (tar paper is budget-friendly)
- Concrete or gravel for the base (optional, but recommended for stability)
- Nails or screws
- Wood preservative or sealant
Building Your Lean-To Shed: A Step-by-Step Guide
Okay, let's build! Remember to consult your local building codes before you begin. Safety first!
Step 1: Preparing the Ground:
Clear the area of debris and level the ground. If you are building on concrete or a solid surface, you can skip to Step 2. Otherwise, consider a gravel base for drainage, or a concrete slab for added sturdiness.
Step 2: Building the Frame:
Construct the frame using pressure-treated lumber. The supporting wall will attach to your existing structure, so make sure your measurements are accurate here. Ensure the frame is level and square. Use corner braces for extra stability.
Step 3: Adding the Walls (if needed):
If your lean-to doesn't directly attach to a wall, you'll need to build walls. Attach plywood or other sheeting to the frame. Remember to leave space for a door or access point.
Step 4: Constructing the Roof:
The roof is the key element of a lean-to. This is usually a simple sloped design. You'll need to construct rafters and secure them to the frame. Attach roofing felt or your chosen roofing material to protect the shed from the elements.
Step 5: Finishing Touches:
Add a door, if necessary. Paint or stain the exterior for protection and aesthetics. Consider adding simple shelving inside.
Tips for Keeping Costs Down:
- Repurpose materials: Look for free or cheap materials from friends, family, or local construction sites.
- Shop around: Compare prices from different lumber yards and hardware stores.
- Buy in bulk: Often you can save money by buying materials in larger quantities.
- Ask for help: Get friends or family to assist with the build to save on labor costs. (Plus, it's more fun!)
Commonly Asked Questions:
Q: Do I need a building permit?
A: It depends on your local building codes. Check with your local authority before you start building.
Q: How long does it take to build a lean-to shed?
A: This varies greatly depending on the size and complexity, but a simple shed can be built in a weekend with some help.
Q: What kind of foundation do I need?
A: A gravel base is often sufficient, but a concrete slab provides a more permanent and stable solution.
Q: Can I build this shed by myself?
A: While possible, having a helper is highly recommended, especially for lifting and securing heavier materials.
Building your own lean-to shed is a rewarding project. By following these steps and tips, you can create a functional and affordable addition to your property that will serve you well for years to come. Happy building!
DIY Lean-To Shed Build: Plans for Organizing Your Outdoor Space

DIY Lean-To Shed Build: Plans for Organizing Your Outdoor Space
Tired of clutter overflowing your garage and backyard? Yearning for a dedicated space to store your gardening tools, outdoor furniture, or even a workshop? Building a lean-to shed offers a fantastic solution, providing extra storage while adding a touch of rustic charm to your property. This guide will walk you through the process, empowering you to create a customized outdoor haven with your own two hands.
Planning Your Lean-To Shed
Before grabbing your tools, careful planning ensures a successful build. Start by determining the shed's purpose. Will it house gardening equipment, bicycles, or something else? This dictates its size and features. Measure your available space â" consider proximity to power sources, drainage, and any existing structures you might attach the lean-to to. Next, sketch a detailed plan, including dimensions, materials list, and a step-by-step construction sequence. Consider the local building codes and acquire the necessary permits if required. Don't underestimate this step; a well-thought-out plan saves time and headaches down the line.
Choosing the Right Location
Selecting the ideal location is crucial. Consider sunlight exposure for natural lighting and ventilation. Assess the ground for levelness and drainage to prevent water accumulation and foundation issues. Proximity to an existing structure, like a house or fence, simplifies construction and provides support. Think about accessibility â" you'll need easy access to transport materials and use the shed comfortably.
Gathering Your Materials
Compile a comprehensive materials list. This will vary depending on your lean-to's size and design, but typically includes pressure-treated lumber for the frame and posts, roofing materials (e.g., asphalt shingles, corrugated metal), fasteners (nails, screws), concrete for the foundation (optional), and any desired finishing touches, such as paint or sealant. Precise measurements are vital to avoid costly mistakes and material waste. Purchase materials in advance to avoid project delays.
Construction: A Step-by-Step Guide
Once your planning is complete, it's time to build! Begin by preparing the foundation. This could be a simple gravel base, a concrete slab, or even attaching the lean-to directly to an existing structure. Next, erect the frame, ensuring plumb and square measurements at every stage. Start with the support posts, then add the roof rafters. Use a level frequently to ensure accuracy. Remember to follow your detailed plan meticulously. Constructing the frame accurately lays the foundation for a strong and durable shed.
Framing and Roofing
Accurate framing is key to a successful lean-to shed. Use pressure-treated lumber to prevent rot and decay. Ensure all joints are tightly secured with appropriate fasteners. For the roof, install rafters with a sufficient slope to allow for proper water drainage. Choose roofing material suitable for your climate and aesthetic preferences. Secure the roofing material thoroughly to prevent leaks. A sturdy, well-constructed roof safeguards your belongings from the elements.
Finishing Touches
Once the structure is complete, add finishing touches to enhance functionality and aesthetics. This could include adding a door, windows, or shelves. Consider painting or staining the wood to protect it from the elements and improve its appearance. Seal any gaps or cracks to prevent water damage. These details elevate the shed from a simple structure into a useful and attractive addition to your outdoor space.
Tips for Success
Building a lean-to shed is a rewarding project, but remember these tips:
- Work safely: Always wear appropriate safety gear, including safety glasses and work gloves.
- Take breaks: Avoid fatigue by taking regular breaks throughout the construction process.
- Ask for help: Don't hesitate to enlist a friend or family member for assistance with heavier tasks.
- Enjoy the process: Building your own shed is a fulfilling experience. Take pride in your handiwork!
By following these steps, you can confidently build a functional and attractive lean-to shed, transforming your outdoor space and providing valuable extra storage. So, gather your tools, and get started on creating your own personalized outdoor haven!
How to Build a DIY Pallet Shed for Your Tools and Equipment
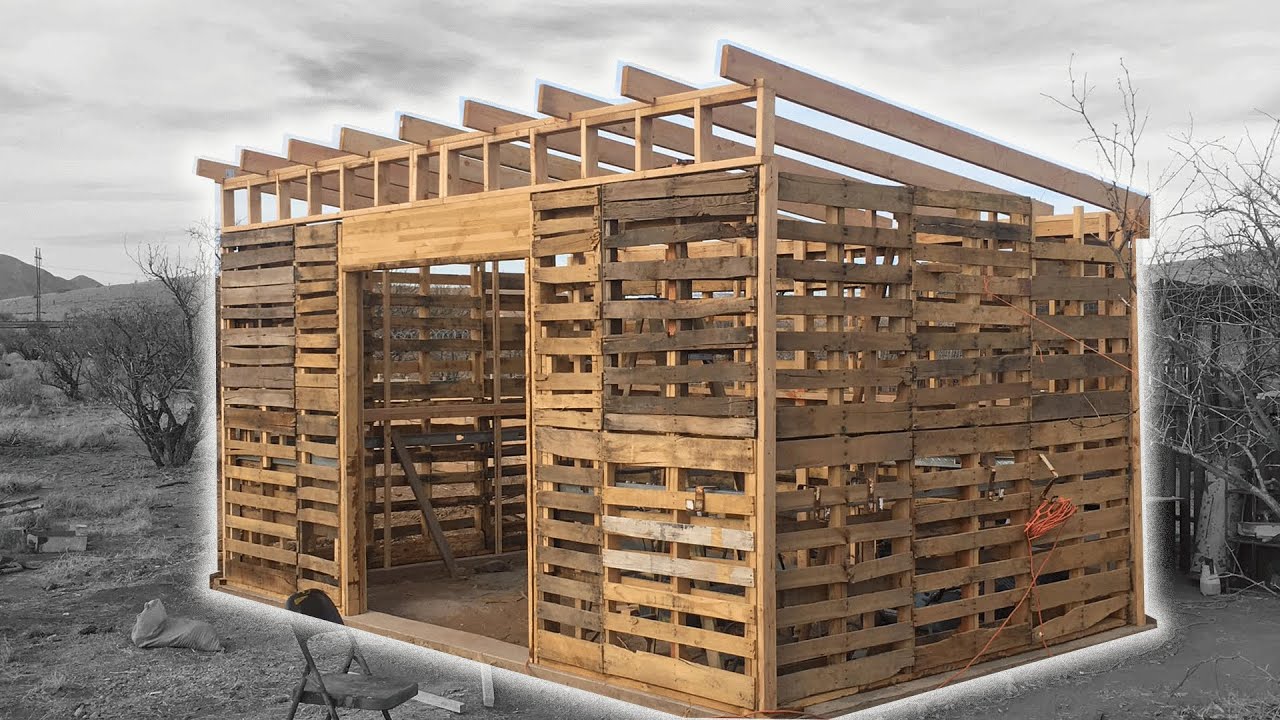
Building Your Dream Pallet Shed: A DIY Guide
Hey there, fellow DIY enthusiasts! So you're thinking about building a shed, but the prices at the big box stores are making your eyes water? I get it. Thatâs why I'm here to show you how to build a fantastic, functional, and surprisingly affordable shed using reclaimed pallets. Let's get started on your very own pallet shed project!Planning Your Pallet Shed Paradise
Before you even think about touching a hammer, some planning is crucial. This isn't rocket science, but a little foresight will save you headaches (and maybe even some sore muscles) down the line.Choosing the Right Pallets
Not all pallets are created equal. You're going to want to source pallets that are in relatively good condition. Look for pallets made of sturdy wood, free of rot, significant cracks, or excessive insect damage. Heat-treated pallets (marked with HT) are generally safer than those treated with methyl bromide (MB). Always check for any markings to ensure they're suitable for your project. Remember, safety first!Size and Location
Think about how much storage you actually need. A tiny shed might seem cost-effective initially, but you could quickly outgrow it. Measure the space you have available and plan accordingly. Consider factors like access â" will you need to maneuver large equipment in and out? Also, think about the shedâs location â" is it level ground? Is it reasonably close to a power source if you want lighting or power tools inside?Design and Materials
While you're building with reclaimed materials, you still need a plan! Sketch out a simple design, noting dimensions, door placement, and any windows you might want to include. Beyond the pallets, you'll need things like:- Screws: Lots of them! Get a variety of sizes to accommodate different wood thicknesses.
- Hammer and Claw Hammer: For those inevitable mishaps (or for just hammering in stubborn nails).
- Drill and Drill Bits: Makes life so much easier than just using a screwdriver.
- Measuring Tape and Level: Essential for accurate construction.
- Safety Glasses and Work Gloves: Always prioritize safety!
- Post Supports (optional): For added stability, especially if your ground isn't perfectly level.
- Roofing Material: Consider using corrugated metal roofing sheets or even recycled materials like tarps, but make sure it's weather resistant.
- Wood Preservative (optional): To extend the life of your pallet wood.
- Door Hardware: Hinges, a latch, maybe even a padlock.
Construction Time!
Alright, let's build! This is a general guideline; your specific steps might vary based on your design.The Foundation
Start with a level base. You can use compacted gravel, concrete blocks, or even a simple wooden frame. The more level your foundation, the more stable your shed will be.The Walls
This is where your pallet magic happens! Begin by carefully cleaning your pallets. Remove any loose nails or debris. Then, start assembling the walls by connecting pallets vertically or horizontally depending on your design. Use screws to secure the pallets together. This is where having a drill is very helpful.The Roof
Construct your roof frame using sturdy 2x4s or similar lumber. This will support your roofing material. Remember to make the roof sloped to allow for proper water drainage. Once the frame is complete, attach your chosen roofing material.The Door
Cut out a section for your door. You can repurpose a section of a pallet for the door itself or use a piece of plywood. Hang your door using appropriate hinges.Finishing Touches
Once the structure is complete, you can add finishing touches like paint (exterior-grade, of course!), additional bracing for extra strength, and any other personal touches to make your shed truly your own.Maintenance and Upkeep
Your beautiful, DIY pallet shed isn't completely maintenance-free. To keep it looking great and lasting a long time:- Regular Cleaning: Sweep out the shed periodically to remove debris and prevent pest infestations.
- Weather Protection: Keep an eye out for any signs of water damage or deterioration, and address them promptly.
- Pest Control: Regularly inspect the shed for signs of insects or rodents. Apply preventative measures as needed.
- Resealing/Painting (as needed): Depending on the weather and your chosen materials, you may need to repaint or reseal the wood every few years to protect it from the elements.
Commonly Asked Questions
Q: How long does it take to build a pallet shed?
A: That depends on the size and complexity of your design, and of course your experience level! A small shed could be completed in a weekend, while a larger, more complex design might take several weekends.
Q: Are pallet sheds structurally sound?
A: When built correctly, using properly selected pallets and sturdy construction techniques, pallet sheds can be very sturdy. However, it's important to ensure the pallets are in good condition and the construction is sound.
Q: Are there any permits required to build a pallet shed?
A: This varies by location. Check with your local building department to see if any permits are required for sheds of your size and design. It's always best to be safe and comply with local regulations.
Q: Can I use treated pallets?
A: While possible, it's generally best to avoid using chemically treated pallets (especially those treated with chromated copper arsenate or CCA). The chemicals can be hazardous. Heat-treated pallets (HT) are a safer option.
Q: What kind of roof is best for a pallet shed?
A: A simple gable roof is a popular and practical choice for pallet sheds. It provides good water runoff and is relatively easy to construct.
There you have it! Building a pallet shed is a rewarding project that can save you a significant amount of money while giving you a personalized storage solution. Remember to prioritize safety, plan ahead, and have fun with it! Let me know if you have any other questions in the comments below. Happy building!How to Build a Lean-To Shed: Create an Affordable Shed for Your Yard

How to Build a Lean-To Shed: Create an Affordable Shed for Your Yard
Constructing a lean-to shed offers a practical and economical solution for expanding storage or creating sheltered workspace within your yard. This guide provides a comprehensive overview of the planning, materials selection, and construction process involved in building an affordable yet durable lean-to structure. The focus will be on a straightforward design suitable for DIY enthusiasts with basic carpentry skills. This project requires careful planning and execution to ensure structural integrity and longevity.
Phase 1: Planning and Design
Before initiating construction, meticulous planning is crucial. This phase involves several key steps that will determine the final outcome and efficiency of the project.
1.1 Site Selection and Assessment
The location of your lean-to shed is paramount. Consider the following factors:
- Proximity to existing structures: Choose a location that allows easy access and minimizes disruption to existing landscaping or buildings. Ideally, attaching the lean-to to an existing wall or fence can simplify construction.
- Sunlight and shade: Assess the amount of sunlight and shade the area receives throughout the day. This impacts the interior temperature and the potential need for additional ventilation.
- Ground conditions: Examine the ground for stability and potential drainage issues. Level ground is ideal, and poor drainage might necessitate additional groundwork.
- Local regulations: Check with your local council or homeowner's association regarding building permits and zoning restrictions. These regulations may dictate size limitations, materials, and setback requirements.
1.2 Dimensions and Design Considerations
Determine the appropriate dimensions for your lean-to shed based on your storage needs and available space. Consider the following:
- Length and width: The length and width should be proportionate to the supporting structure and the available space. Overly large lean-tos require more robust framing.
- Height: The height should be sufficient for comfortable access and storage, typically ranging from 6 to 8 feet. Higher roofs offer more headroom but require more materials.
- Roof pitch: A gentle roof pitch (around 4:12 or 6:12) is usually sufficient for shedding water effectively. Steeper pitches require more materials but are better at managing snow accumulation.
- Door placement and size: Consider the placement and size of the door for easy access to the shed's interior. Standard door sizes are readily available and cost-effective.
1.3 Materials List and Budget
Creating a detailed materials list is crucial for cost estimation and efficient purchasing. This list should include quantities and specifications for:
- Pressure-treated lumber: For the frame, including posts, beams, rafters, and supports. The grade of lumber should match the structural requirements.
- Plywood or OSB sheathing: For wall and roof cladding. The thickness will depend on the size and intended use of the shed.
- Roofing material: Options range from asphalt shingles to metal roofing, each with varying costs and longevity. Consider local climate conditions when choosing a roofing material.
- Fasteners: Nails, screws, and bolts in appropriate sizes and quantities.
- Hardware: Hinges, door handle, and any additional hardware needed for doors and windows.
- Other materials: Concrete or gravel for the foundation, felt paper or house wrap for waterproofing, and any necessary paint or sealant.
Develop a detailed budget, factoring in the cost of materials, tools, and any potential labor costs if you hire assistance.
Phase 2: Construction
Once the planning phase is complete, the construction process can begin. This involves several critical steps that require precision and attention to detail.
2.1 Foundation Preparation
A solid foundation is essential for the longevity of the lean-to. The complexity of the foundation will depend on the size and weight of the structure. Options include:
- Concrete slab: Offers a durable and level base but requires more effort and material. Ideal for larger lean-tos.
- Gravel base: A simpler and more affordable option, suitable for smaller structures. Provides good drainage but may not be as level as a concrete slab.
- Existing surface: If attaching the lean-to to an existing structure with a solid base, this can eliminate the need for a separate foundation.
Regardless of the chosen method, ensure the foundation is level and adequately compacted.
2.2 Frame Construction
Construct the frame according to your design specifications. This involves assembling the following elements:
- Base frame: Construct a rectangular base frame using pressure-treated lumber. Ensure the frame is square and level.
- Vertical supports: Attach vertical supports (posts) to the base frame at regular intervals. The spacing will depend on the size of the lean-to and the roof load.
- Rafters: Attach rafters to the top of the vertical supports, creating the sloping roofline. Use appropriate fasteners and ensure the rafters are evenly spaced and securely attached.
- Ridge beam (if necessary): For longer lean-tos, a ridge beam may be necessary to support the rafters and improve structural integrity.
Ensure all connections are strong and secure using appropriate fasteners. Regularly check for squareness and levelness throughout the framing process.
2.3 Wall and Roof Sheathing
Once the frame is complete, install the wall and roof sheathing. This involves attaching plywood or OSB sheets to the frame. Ensure proper alignment and secure fastening. Consider adding house wrap for increased weather protection before installing the roofing material.
2.4 Roofing Installation
Install the chosen roofing material according to the manufacturer's instructions. This usually involves laying the roofing material over the sheathing, starting at the bottom and working your way up. Proper flashing around chimneys or other protrusions is critical for preventing leaks.
2.5 Door and Window Installation (if applicable)
If your design includes a door or windows, install them after the wall and roof sheathing are completed. Ensure proper sealing and weatherproofing around the openings to prevent drafts and leaks.
Phase 3: Finishing Touches
After the main construction is complete, add the finishing touches to enhance the aesthetics and functionality of your lean-to shed.
3.1 Exterior Finishing
Apply exterior paint or sealant to protect the wood from the elements and improve the appearance of the shed. Choose a weather-resistant finish suitable for exterior use.
3.2 Interior Finishing (optional)
If desired, add interior finishing such as paint, shelving, or additional insulation to improve the functionality and comfort of the shed's interior.
3.3 Safety Considerations
Always prioritize safety during the construction process. Wear appropriate safety gear, such as safety glasses, gloves, and work boots. Use caution when working at heights and ensure proper support for heavy materials.
Building a lean-to shed is a rewarding project that enhances the functionality and value of your property. By carefully following these steps and prioritizing safety, you can create a durable and affordable storage solution or workspace that will serve you for years to come. Remember to consult local building codes and regulations before commencing construction to ensure compliance.
10x12 Pallet Shed Plans: Transform Recycled Wood into Outdoor Storage

10x12 Pallet Shed Plans: Transform Recycled Wood into Outdoor Storage
This comprehensive guide provides detailed plans for constructing a 10x12 foot pallet shed, utilizing reclaimed wood pallets for a sustainable and cost-effective outdoor storage solution. The project requires careful planning and execution, but the end result is a sturdy, functional structure that minimizes environmental impact and offers significant savings compared to traditional shed construction. This guide outlines the necessary materials, tools, and step-by-step instructions to facilitate successful completion.
I. Planning and Preparation
Before commencing construction, meticulous planning is paramount to ensure a structurally sound and aesthetically pleasing shed. This phase involves several key considerations:
A. Site Selection and Preparation
Selecting an appropriate location is crucial. Consider factors such as:
- Accessibility: Ensure easy access for material delivery and future maintenance.
- Level Ground: A level surface is essential for stability. Uneven ground will require leveling prior to construction.
- Drainage: Choose a location with adequate drainage to prevent water accumulation around the shed.
- Sunlight and Shade: Consider the impact of sunlight and shade on the shed's interior and the materials used.
- Local Regulations: Check local building codes and regulations regarding shed construction and permits.
Once the location is selected, prepare the ground by clearing vegetation, removing debris, and leveling the surface. Consider using a compacted gravel base for improved drainage and stability.
B. Pallet Acquisition and Assessment
Sourcing high-quality pallets is critical to the project's success. Consider these factors:
- Condition: Select pallets that are structurally sound, free from significant rot, insect infestation, and major damage.
- Type of Wood: Identify the type of wood used in the pallets. Hardwoods like oak or pine are preferable for their durability.
- Heat Treatment: Ensure the pallets are heat-treated (HT) or methyl bromide-fumigated (MB) to meet international phytosanitary standards. This prevents the introduction of invasive pests.
- Quantity: A 10x12 foot shed will require a substantial number of pallets. Accurate estimation is crucial to avoid delays.
Thoroughly inspect each pallet before incorporating it into the structure. Discard any pallets exhibiting significant damage or signs of decay.
C. Material and Tool Acquisition
Beyond the pallets, additional materials and tools are necessary:
- Foundation Materials: Concrete blocks, gravel, or pressure-treated lumber for the base.
- Fasteners: Galvanized nails, screws, and possibly lag bolts for robust connections.
- Plywood or OSB: For sheathing the walls and roof.
- Roofing Material: Asphalt shingles, metal roofing, or other suitable material.
- Door and Window Materials: Reclaimed wood, or new materials for doors and windows.
- Paint or Stain (Optional): For weather protection and aesthetic enhancement.
The necessary tools include:
- Measuring Tape and Level: For accurate measurements and ensuring level surfaces.
- Hammer and Claw Hammer: For driving nails and removing them.
- Drill and Screwdriver Bits: For driving screws and creating pilot holes.
- Circular Saw or Hand Saw: For cutting wood to size.
- Safety Glasses and Gloves: For personal protection.
- Shovel and Rake: For ground preparation.
II. Construction Process
The construction process can be divided into several distinct phases:
A. Foundation Construction
Construct a stable and level foundation. Options include a concrete slab, a gravel base with pressure-treated lumber framing, or a concrete block foundation. The chosen foundation must be capable of supporting the weight of the shed and its contents.
B. Pallet Preparation and Assembly
Disassemble the pallets carefully, removing any loose or damaged components. Clean the pallets thoroughly to remove dirt, debris, and any potential hazards. Sort the usable wood by size and condition. The pallets will be used to create the shed's walls and roof structure. Consider using additional lumber for reinforcement where necessary.
C. Wall Construction
Construct the shed's walls using the prepared pallet wood. This may involve creating a frame from stronger pallet components and then filling the frame with other pallet pieces. Ensure the walls are plumb and square. Use additional bracing for stability. The walls should be assembled on the ground for easier handling before being raised onto the foundation.
D. Roof Construction
The roof structure should be designed to withstand local weather conditions. Consider using a simple gable or shed roof design. Utilize the pallet wood to create the roof trusses and rafters. Ensure proper overhang to protect the walls from rain and snow. Sheathe the roof with plywood or OSB, and then install the chosen roofing material.
E. Door and Window Installation
Install the doors and windows, ensuring a secure and weathertight fit. Use appropriate sealing and weatherstripping materials to prevent drafts and water infiltration.
F. Finishing Touches
Once the structure is complete, apply a protective coat of paint or stain to extend the lifespan of the wood and enhance its aesthetic appeal. Consider adding additional features such as shelving, ventilation, or a lock for enhanced functionality and security.
III. Safety Considerations
Safety is paramount throughout the construction process. Always wear appropriate safety gear, including safety glasses, gloves, and work boots. Use caution when handling power tools and follow all manufacturer's instructions. Ensure the work area is well-lit and free from obstructions. Seek assistance if needed for lifting heavy materials or performing complex tasks.
IV. Conclusion
Building a 10x12 foot pallet shed is a rewarding project that combines sustainability with cost-effectiveness. By following these detailed plans and prioritizing safety, you can create a durable and functional outdoor storage solution. Remember to adapt these plans to your specific needs and local conditions, always prioritizing structural integrity and safety. The process requires effort and attention to detail, but the result is a unique and environmentally conscious structure that serves as a testament to resourcefulness and ingenuity.
DIY Wood Pallet Shed: A Beginner-Friendly Guide to Shed Construction
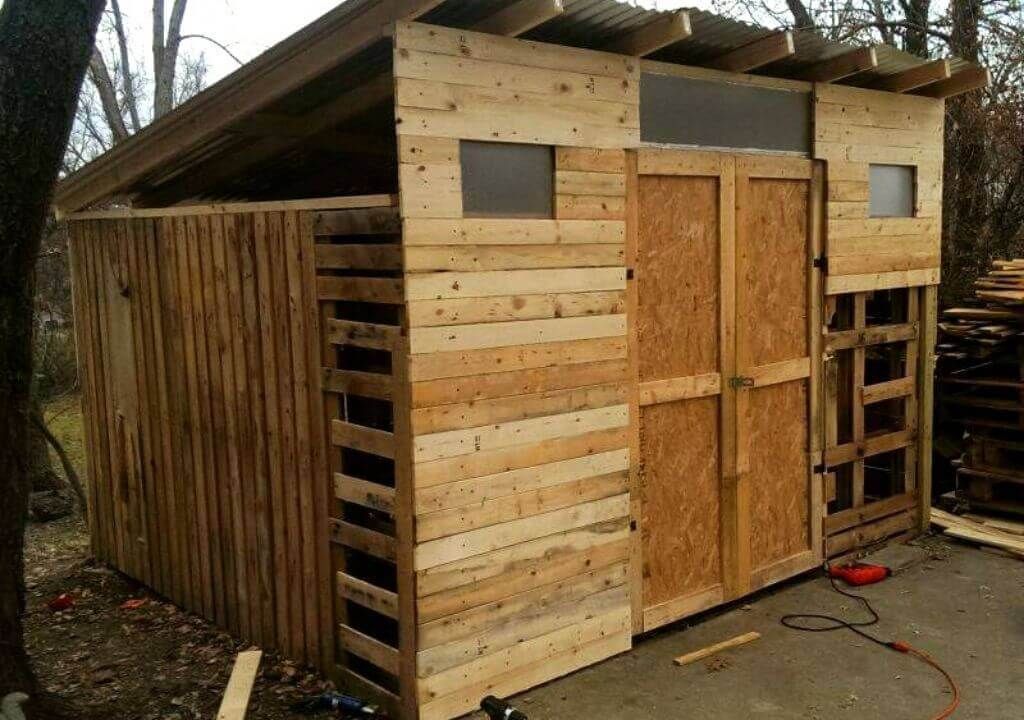
DIY Wood Pallet Shed: A Beginner-Friendly Guide to Shed Construction
Constructing a shed from reclaimed wood pallets presents a cost-effective and environmentally conscious alternative to purchasing a pre-fabricated structure. This guide provides a comprehensive, step-by-step approach for beginners, emphasizing safety and best practices throughout the process. While utilizing reclaimed materials offers significant financial advantages, careful planning and execution are crucial for a structurally sound and aesthetically pleasing result.
I. Planning and Preparation: Laying the Foundation for Success
Before commencing construction, thorough planning is paramount. Neglecting this stage can lead to significant complications and potential project failure. This phase encompasses several key aspects:
A. Shed Design and Dimensions
Determine the desired dimensions of your shed based on your storage needs. Consider factors such as the number and size of items to be stored, and available space in your yard. Sketch a basic plan outlining the overall dimensions, door placement, and window placement (if desired). Simple rectangular designs are recommended for beginners. Remember to adhere to local building codes and regulations regarding shed size and placement.
B. Pallet Acquisition and Assessment
Sourcing suitable pallets is a critical step. Inspect pallets thoroughly for damage, rot, or infestation. Prioritize pallets constructed from pressure-treated lumber, as this offers superior durability and resistance to the elements. Avoid pallets displaying signs of significant wear, decay, or chemical contamination. Ideally, aim for pallets of uniform size and quality to simplify the construction process. You will need to calculate the quantity of pallets required based on your shedâs design.
C. Site Preparation and Foundation
Select a level and well-drained location for your shed. Clear the area of debris, vegetation, and any obstacles. The foundation is crucial for structural integrity; a concrete slab offers the most robust and durable foundation. Alternatively, you can create a gravel base, ensuring proper leveling and compaction. The chosen foundation must be adequately sized to support the weight of the completed shed.
D. Material Gathering and Tool Preparation
Beyond pallets, gather necessary materials such as: screws, nails, wood glue, weatherproofing sealant, roofing materials (e.g., asphalt shingles, metal sheeting), and any desired hardware (e.g., hinges, door handle, window latches). Ensure you have the appropriate tools: a hammer, saw (circular saw or hand saw), drill, screwdriver, measuring tape, level, safety glasses, work gloves, and a pry bar for dismantling pallets.
II. Construction Phase: Assembling the Pallet Shed
This section details the construction process, assuming a basic rectangular shed design. Adapt these instructions as needed for more complex designs.
A. Pallet Disassembly and Preparation
Carefully dismantle the pallets, removing any nails or staples. Inspect each board for damage and discard any unsuitable pieces. Clean the boards, removing any dirt, debris, or loose splinters. You may need to cut some boards to fit your design specifications. Remember to wear safety glasses and gloves during this process.
B. Floor Construction
Construct the floor frame using the prepared pallet boards. Create a rectangular frame matching your shed's dimensions, securely fastening the boards using screws and wood glue. This frame will provide a solid base for the floor. Lay additional boards across the frame, creating a sturdy and even floor surface. Ensure proper spacing between boards to allow for drainage.
C. Wall Construction
Construct the walls using the pallet boards, arranging them vertically to create a visually appealing and structurally sound wall. Use screws and wood glue to secure the boards to the floor frame. Ensure the walls are plumb and square. For added stability, consider adding vertical supports inside the walls. Repeat this process for all four walls.
D. Roof Construction
Construct the roof frame using pallet boards or other suitable lumber. Design the roof with an appropriate pitch for water runoff. Securely fasten the roof frame to the top of the walls. Install the chosen roofing material, ensuring proper overlapping and sealing to prevent leaks. Use appropriate fasteners for your roofing material.
E. Door and Window Installation
Cut an opening in one of the walls for the door. Construct the door frame and attach the door. Install hinges and a handle. If incorporating windows, create openings in the desired locations and install the windows using appropriate sealant and fasteners.
III. Finishing Touches: Enhancing Aesthetics and Durability
Once the basic structure is complete, several finishing touches can enhance both the aesthetics and longevity of your shed.
A. Weatherproofing
Apply a weatherproofing sealant to all exposed wood surfaces to protect against moisture damage. This will significantly extend the lifespan of your shed and enhance its resistance to the elements. Choose a sealant appropriate for exterior use and follow the manufacturer's instructions.
B. Painting or Staining
Consider painting or staining the exterior of the shed to improve its appearance and provide additional protection from the elements. Choose a paint or stain designed for exterior use and follow the manufacturer's instructions for application. This step adds a personal touch and enhances the overall curb appeal.
C. Interior Finishing
If desired, add interior finishing touches such as shelving, pegboards, or additional storage solutions. This will maximize the usability of your shed and create a more organized storage space.
IV. Safety Precautions: Prioritizing Safety Throughout the Process
Safety should be a paramount concern throughout the construction process. Observe the following precautions:
By following this comprehensive guide, beginners can successfully construct a durable and aesthetically pleasing wood pallet shed. Remember that patience, meticulous planning, and attention to detail are key to achieving a successful outcome. Enjoy the process and the satisfaction of creating a functional and attractive addition to your property.
Friday, November 15, 2024
12x20 Shed with Loft: Ideal for Outdoor Hobbyists

Unlock Your Potential: A 12x20 Shed with Loft â" The Perfect Hobby Haven
Imagine a dedicated space, entirely your own, where creativity flows freely and projects blossom. No more cramming your hobbies into a cluttered garage or spare bedroom. A 12x20 shed with a loft offers the ultimate solution for outdoor enthusiasts and hobbyists seeking a personalized workshop or studio. This versatile structure provides ample room for your tools, materials, and finished projects, while the added loft maximizes storage and functionality. Let's explore why a 12x20 shed with a loft represents the ideal investment for your passion.
Ample Space for Your Growing Collection
The generous 12x20 footprint provides a significant amount of floor space, easily accommodating even the most extensive hobby collections. Whether you're a woodworker meticulously crafting intricate furniture, a painter with easels and canvases aplenty, or a gardener organizing seeds and tools, this shed offers the room to spread out and work comfortably. No more feeling cramped or frustrated by a lack of space. Youâll find yourself enjoying the process more when you have adequate room to maneuver and organize.
Customizable Interior Design
Design your shed's interior to perfectly suit your needs. Install sturdy workbench with ample storage drawers, add overhead shelving for smaller items, and strategically position your tools and equipment for easy access. Consider incorporating specialized features based on your specific hobby, like a dedicated area for mixing paints, a potting bench for gardening enthusiasts, or a display case for showcasing finished projects. The possibilities are truly endless.
The Loft: A Treasure Trove of Storage
The loft adds an entirely new dimension to your shed's functionality. This valuable extra space provides ideal storage for less frequently used items, keeping your main workspace clutter-free and organized. Imagine storing seasonal decorations, extra tools, bulky materials, or even finished projects awaiting display. The loft transforms a simple shed into a highly efficient and organized space, optimizing every square foot.
Accessing the Loft with Ease
Modern shed designs often incorporate easy-access lofts via sturdy, retractable ladders or even built-in staircases for added convenience. Think about the comfort and safety aspects when planning your loft access. Choose a solution that works seamlessly with your physical capabilities and the overall design of your shed.
Benefits Beyond the Hobby
Beyond providing a dedicated space for your passion, a 12x20 shed with a loft offers numerous other benefits. It protects your valuable equipment from the elements, provides a secure storage solution for outdoor gear, and can even increase the overall value of your property. It's a smart investment that pays dividends in convenience, organization, and peace of mind.
Key Advantages Summarized:
- Increased storage space with the loft.
- Dedicated workspace for your hobby.
- Protection from the elements for equipment and materials.
- Enhanced property value.
- Improved organization and efficiency.
Investing in a 12x20 shed with a loft is an investment in your passion. It's a chance to create a dedicated and organized space where your creativity can flourish. Transform your hobby from a stressful squeeze into a joyful and productive pursuit. Start planning your dream hobby haven today!
Monday, November 11, 2024
How to Create a Pole Barn with Extra Storage Space

A pole barn, with its robust construction and adaptable design, provides a versatile solution for various needs. While often serving as garages, workshops, or agricultural shelters, incorporating strategic design elements can transform your pole barn into a haven of maximized storage space. This article delves into the key aspects of creating a pole barn with enhanced storage capabilities, guiding you through the planning and construction process.
I. Planning and Design:
1. Define Your Storage Needs:
Inventory Assessment: Before embarking on the design, meticulously assess your storage needs. This involves listing all items you intend to store, considering their dimensions, weight, and special requirements.
Functionality: Consider the purpose of the storage space. Will it be for tools, vehicles, equipment, or a combination thereof? Identifying specific storage needs will dictate the design and layout.
2. Optimize Space Utilization:
Verticality: Maximize storage space by utilizing vertical space. Incorporate high shelves, overhead storage systems, and mezzanines to store less frequently used items above ground level.
Modular Design: Employ modular storage solutions like shelving units, cabinets, and drawers to efficiently organize and access items. These systems can be customized and rearranged to suit changing needs.
Dedicated Zones: Designate specific zones within the barn for various storage categories, such as tools, equipment, vehicles, or seasonal items. This structured approach ensures efficient access and organization.
3. Maximize Accessibility:
Clear Aisleways: Ensure adequate space between storage units and vehicles to allow for easy maneuvering and accessibility.
Door Placement: Strategically position doors to maximize vehicle access and facilitate loading and unloading. Consider a combination of overhead doors and pedestrian entrances for convenient entry.
Lighting: Ample lighting is crucial for safe navigation and efficient storage management. Install high-quality lighting throughout the barn, with a focus on illuminating storage areas.
4. Enhance Durability and Sustainability:
Building Materials: Opt for durable materials resistant to moisture, pests, and temperature fluctuations. Metal siding and roofing, treated lumber, and high-quality insulation will ensure long-term longevity.
Energy Efficiency: Consider incorporating energy-efficient features, such as insulation, ventilation, and natural lighting, to minimize energy consumption and reduce operating costs.
II. Construction and Implementation:
1. Foundation and Framing:
Concrete Piers: For pole barns, concrete piers provide a solid and durable foundation. Ensure adequate spacing and depth to support the load of the structure.
Pole Construction: Utilize pressure-treated lumber or steel poles for framing, ensuring they are securely anchored to the concrete piers.
Roof System: Choose a robust roof system, such as a truss system, to support potential storage loads and withstand environmental conditions.
2. Enclosing the Structure:
Walls and Roof: Install walls and roof panels using durable materials like metal siding and roofing. Consider adding insulation for temperature regulation and noise reduction.
Windows and Doors: Install windows and doors according to the desired level of light and ventilation. Include doors large enough to accommodate vehicles and equipment.
3. Interior Finishing and Storage Systems:
Flooring: Opt for durable flooring that can withstand heavy loads and potential spills. Concrete, epoxy-coated floors, or timber decking offer suitable options.
Shelving and Storage: Install shelving units, cabinets, and drawers to maximize storage capacity. Consider adjustable shelves, overhead storage systems, and pull-out drawers for easy access.
4. Electrical and Mechanical Systems:
Electrical Wiring: Install electrical wiring to power lighting, outlets, and any specialized equipment. Consider dedicated circuits for high-power appliances.
Ventilation and Heating/Cooling: Incorporate adequate ventilation for proper air circulation, especially for areas with high humidity or potential for dust accumulation. Consider installing heating or cooling systems as needed.
III. Maintenance and Organization:
1. Regular Maintenance:
Inspect Foundation and Structure: Regularly inspect the foundation and structural elements for any signs of damage or deterioration.
Clean and Maintain Storage Systems: Regularly clean and maintain storage systems to prevent dust accumulation, moisture damage, and pest infestations.
Monitor Ventilation and Temperature: Ensure proper ventilation and temperature control to prevent moisture buildup and damage to stored items.
2. Organizing and Labeling:
Clear Labeling: Label storage units and shelves clearly to facilitate efficient access and organization.
Regular Decluttering: Regularly declutter and dispose of unused or obsolete items to maintain optimal storage space.
IV. Considerations for Specific Needs:
1. Vehicle Storage:
Garage Doors: Install large garage doors for easy vehicle access.
Ceiling Height: Ensure adequate ceiling height to accommodate taller vehicles.
Flooring: Choose durable flooring capable of supporting heavy vehicle loads.
2. Workshop Storage:
Workbenches and Storage: Include ample workbenches and storage for tools and equipment.
Electrical Outlets: Provide sufficient electrical outlets for power tools and machinery.
Lighting: Install high-quality lighting to illuminate work areas effectively.
3. Agricultural Storage:
Moisture Control: Employ measures to control moisture levels, especially for storing hay, grain, or other agricultural products.
Pest Control: Implement pest control measures to protect stored products from infestation.
Ventilation: Provide adequate ventilation to prevent moisture buildup and promote air circulation.
Conclusion:
Constructing a pole barn with enhanced storage capacity requires careful planning, thoughtful design, and meticulous implementation. By following these guidelines, you can transform your pole barn into a highly functional and efficient storage solution, maximizing space utilization, accessibility, and durability. From planning your storage needs to ensuring proper maintenance, a well-designed pole barn will serve as a valuable asset for many years to come.
DIY Pole Barn Plans: How to Add Windows and Ventilation

Okay, youâve got your pole barn plan, youâve got your lumber, maybe even your foundation is starting to take shape. But wait, thereâs something missing. Your future barn is looking a little⦠well, dark and stuffy. Itâs time to add some light and life with windows and ventilation!
This is where the fun really begins. Youâve got some choices to make: what kind of windows, how many, and how to get that fresh air flowing through. Donât worry, itâs not as overwhelming as it sounds. Let's break it down.
Windows: The Eyes of Your Barn
First things first, windows. Theyâre more than just a pretty face; theyâll brighten up your space, bring in some natural light, and even help keep things cooler during the warmer months.
Window Style and Size:
- Sliding windows: These are great for easy access, perfect for workshops or areas where you need to move things in and out. Plus, they're pretty affordable.
- Casement windows: They swing open like a door, allowing for a nice breeze. They can add a touch of farmhouse charm and are great for letting in a lot of light.
- Double-hung windows: Classic and reliable, they can be opened at the top or bottom for ventilation. They're a good choice for a more traditional look.
- Fixed windows: These don't open, but they're fantastic for letting in lots of natural light. They're often used in high-traffic areas where you don't need ventilation.
Size: It really depends on the size of your barn and the amount of light you want. Smaller windows are great for letting in some light without compromising wall space, while larger windows can make your barn feel even more spacious.
Window Placement:
- Think about the sun's path: Position windows to maximize natural light and warmth during the day. You might want to place them on the south side for the best sunlight.
- Consider your needs: Do you need windows for a workshop? Maybe you need them for a horse stall? Think about how you'll use the space and place them accordingly.
Ventilation: Breathing Room for Your Barn
Now, let's talk ventilation. It's essential for keeping your barn dry, free of moisture, and comfortable to work in.
Types of Ventilation:
- Ridge vents: These run along the peak of your roof, allowing hot air to escape. They're a great choice for general ventilation and help prevent moisture buildup.
- Soffit vents: Located under the eaves of your roof, these pull fresh air into the barn. They work best in combination with ridge vents to create a good airflow.
- Gable vents: These are located on the gable ends of your barn, providing a direct way for air to enter and exit. They're a good option for larger barns or those with high ceilings.
- Louvered doors: If you need a lot of airflow, you can add louvered doors to your barn doors. They're also a stylish addition.
- Ceiling fans: A simple and effective way to circulate air, especially during the warmer months.
Ventilation Tips:
- Cross-ventilation: This is the most efficient way to ventilate. It involves having openings on opposite sides of the barn to allow air to flow through.
- Consider the climate: In areas with high humidity, you might need more ventilation than in drier climates.
- Don't forget the animals: If you're housing animals, ensure you have adequate ventilation to keep them cool and comfortable.
DIY or Hire It Out?
The great thing about pole barns is that they're often relatively simple to build, even with some added features like windows and ventilation. If you're comfortable with basic carpentry and construction, you can certainly handle this yourself.
Here's what you'll need:
- Tools: A circular saw, jigsaw, drill, level, tape measure, safety glasses, gloves, and a ladder.
- Materials: Windows, vent covers, flashing, screws, sealant, and any necessary trim.
Follow these steps for adding windows and ventilation:
1. Plan your placement: Mark the locations for your windows and vents on the exterior walls.
2. Cut the openings: Carefully cut out the openings for your windows and vents using a circular saw or jigsaw.
3. Install the windows: Place the windows in the openings, secure them with screws, and apply sealant around the edges.
4. Install the vents: Attach the vent covers to the openings, ensuring they are properly secured and aligned.
5. Add flashing: Apply flashing around the windows and vents to prevent water from seeping in.
6. Finishing touches: Add trim around the windows and vents for a more polished look.
If you're feeling unsure about tackling these steps, don't hesitate to hire a professional contractor. They'll ensure that the windows and ventilation are properly installed and that your barn is well-ventilated and protected from the elements.
Time to Light It Up!
Adding windows and ventilation to your pole barn is a great way to make it more functional, comfortable, and visually appealing. Itâs a relatively simple project that can be done with some DIY skills or by hiring a professional.
So, get those plans ready, grab your tools, and let the light and fresh air flow into your new pole barn!
DIY Pole Barn: How to Add a Porch or Overhang for Extra Space

Okay, you've got your awesome pole barn, but you're thinking it could use a little something extra, right? Maybe a space to relax, enjoy the view, or maybe just have a little more room for those weekend projects. Well, good news, my friend! You can easily add a porch or overhang to your pole barn and give it a whole new dimension.
Let's dive in and break down how to build that porch:
Step 1: The Big Picture - Planning Your Porch
Before you grab your tools, take a step back and visualize your dream porch. Here's what you need to consider:
Size and Shape: How big do you want your porch to be? Do you want it attached to one side, or wrapping around a corner? Maybe a sweet little balcony? The size and shape are all up to you!
Design: Do you want a traditional, covered porch with a roof, or a more open, breezy design?
Location: Think about the best spot for your porch. Do you want it to face the sunset, or maybe offer a view of your garden?
Materials: Wood, metal, concrete? Choose the materials that fit your budget and style.
Permits: Always check with your local building department to see if you need permits for your porch project.
Step 2: Foundation and Framing â" The Strong Base of Your Porch
Okay, now it's time to get your hands dirty! Here's how to build a solid foundation for your porch:
Foundation: For a sturdy and long-lasting porch, a concrete foundation is the way to go. You can hire a contractor to pour the foundation, or DIY it yourself. Just make sure it's level and strong enough to support the weight of your porch.
Framing: Once the foundation is set, you can start building your porch's frame. Use pressure-treated lumber for the bottom plates and posts for a strong and long-lasting frame.
Step 3: The Roof â" Keeping You Dry and Stylish
The roof is the heart of a porch, and it protects you from the elements. Here's how to build a fantastic roof:
Roof Trusses: For a strong and stable roof, use pre-engineered roof trusses. They're easy to install and create a solid structure.
Roofing Materials: You've got options! Shingles, metal roofing, or even a cool green roof? Choose the style that best suits your porch and your budget.
Step 4: Deck and Railings â" The Finishing Touches
Now for the fun part! Building the deck and adding some railings to keep things safe and stylish.
Decking: Choose your decking material wisely. Wood, composite, or even recycled plastic? Consider the look and longevity when you choose.
Railings: Don't forget about safety! Build strong and stylish railings using sturdy wood or metal.
Stairs: If you have a raised porch, you'll need stairs for easy access. Make sure they are wide enough for comfortable use.
Step 5: Finishing Touches â" Making Your Porch Shine
Almost done! Now, it's time to add those finishing touches that will make your porch feel like home.
Lighting: Add some warm lighting for a cozy atmosphere. Pendant lights, string lights, or lanterns - let your creativity shine!
Furniture: Make it inviting with comfy furniture. Adirondack chairs, a swing, or even a dining table â" choose what suits your style.
Plants: Add some greenery to your porch for a touch of nature. Vines climbing up the posts, potted flowers, or a small herb garden will add life and beauty.
Decor: Personalize your porch with your favorite decorations. Weatherproof cushions, lanterns, and artwork will make it uniquely yours.
Pro Tips for a Successful Porch Project:
Measure twice, cut once: You know the drill! Accuracy is key for a smooth and successful build.
Safety First: Wear appropriate safety gear, like goggles, gloves, and work boots.
Don't Rush: Building a porch takes time. Take your time, enjoy the process, and make sure everything is done right.
Beyond a Porch: Adding an Overhang to Your Pole Barn
If a full-blown porch isn't what you're after, adding an overhang to your pole barn is a great way to create a sheltered area without a lot of fuss. Here's how:
Install beams: Attach sturdy beams to the existing poles of your barn, extending them outward.
Add a roof: Place a roof directly on top of the beams. You can use the same roofing materials as your main barn roof.
Create a space: This overhang can become a covered patio, a shaded spot for your car, or even a storage area.
The Bottom Line
Building a porch or an overhang on your pole barn is a fantastic way to expand your space, increase your enjoyment of the outdoors, and add some personality to your property. It's a project you can be proud of, and one that will bring you joy for years to come. Remember to enjoy the process, and don't be afraid to get creative! Happy building!
How to build a functional 10x12 garden shed from scratch
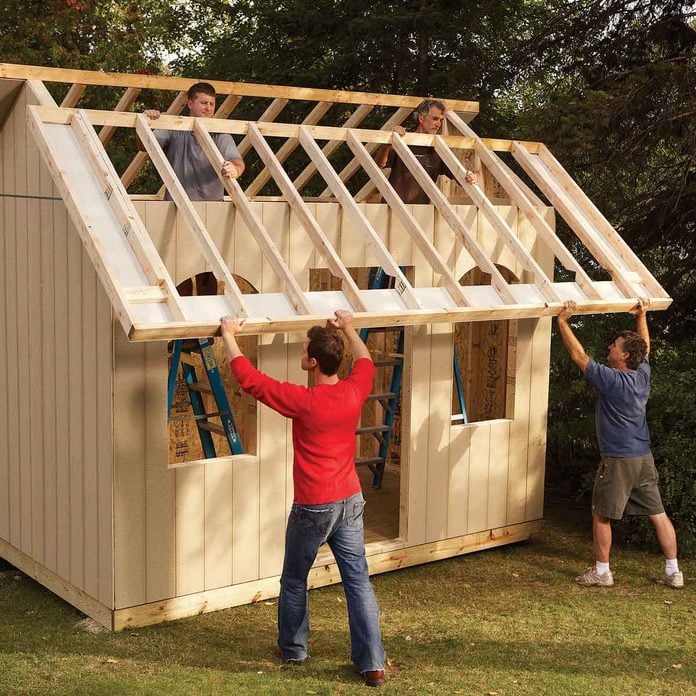
Alright, you've finally decided to take the plunge. You're going to build your own garden shed! I'm with you - a well-built shed can be a lifesaver, a sanctuary, and an amazing addition to your backyard. But let's be honest, it can also seem pretty daunting. Don't worry, I'm here to help.
This guide will walk you through building a functional 10x12 shed from scratch. We'll cover everything from planning and materials to the final touches. So grab a cup of coffee, put on your favorite construction playlist, and let's get building!
Step 1: The Blueprint - Planning Your Paradise
First things first, let's get that blueprint in order. You want to make sure your shed is the perfect size and shape for your needs. Here's what to consider:
Location, location, location! Choose a level spot with good drainage. Make sure it's accessible and away from any power lines or trees.
Size matters. A 10x12 shed is a great size for most purposes. But consider what you'll be storing. Do you need extra space for a workbench, lawnmower, or even a small refrigerator?
Style and design. Do you want a traditional shed, a modern one, or something with a unique style? Check out some online resources for inspiration!
Building codes. Before you start, double-check local building codes. They can vary from place to place, so it's always best to be safe.
Step 2: The Foundation - A Strong Base for Your Shed
Now that you've got your blueprint, it's time to think about the foundation. There are a few different options, so choose the one that best suits your needs:
Concrete slab: The most durable and long-lasting option. You'll need to pour a concrete slab that's at least 4 inches thick and reinforced with rebar.
Pressure-treated wood piers: A good alternative to concrete. Set the piers on a bed of gravel, ensuring they are level and plumb.
Concrete blocks: Easy to lay and relatively inexpensive. Make sure to use blocks that are specifically designed for building foundations.
Step 3: Framing - The Backbone of Your Shed
With the foundation in place, you can start framing the walls and roof. Here's the breakdown:
Floor joists: Use pressure-treated lumber for your floor joists. They need to be spaced 16 inches apart and securely fastened to the foundation.
Wall studs: These are the vertical supports for your walls. They should be 2x4s spaced 16 inches apart.
Roof rafters: The rafters form the triangular shape of your roof. You'll need to determine the roof pitch and spacing for the rafters, which is often determined by local building codes.
Sheathing: This is the material that covers the framing and provides support for the roofing and siding. You can use plywood, OSB, or even composite sheathing.
Step 4: Roofing - A Safe and Secure Cover
Time to give your shed a roof! Here are the main steps:
Underlayment: This is a waterproof layer that goes under the shingles. It protects the sheathing from moisture and adds extra protection.
Shingles: Choose the type of shingles that best suits your needs and budget. Asphalt shingles are the most common and affordable.
Flashing: This is metal or plastic material that helps direct water away from the edges of the roof. You'll need flashing around chimneys, vents, and other roof penetrations.
Step 5: Siding - Adding Style and Protection
The siding not only looks good, it protects your shed from the elements. Here are some popular choices:
Vinyl siding: Durable, low-maintenance, and comes in a wide variety of colors.
Wood siding: A classic look that can be painted or stained.
Fiber cement siding: Resistant to moisture, insects, and fire.
Step 6: Doors and Windows - Entrance and Airflow
Now for the finishing touches:
Doors: Choose a durable door that fits your shed's size and style. You can opt for single or double doors, depending on your needs.
Windows: Adding windows allows natural light into the shed and improves ventilation. Choose the size and number of windows based on your preferences.
Step 7: Interior - Make it Your Own
Now it's time to make your shed a personal space!
Flooring: You can choose from a variety of flooring options, such as wood, tile, or concrete.
Shelving and storage: This is the fun part! Add shelving, hooks, and other storage solutions to organize your belongings.
Electricity: If you want to add electricity to your shed, you'll need to consult with an electrician.
Step 8: Finishing Touches - The Cherry on Top
You're almost there! Here are some final touches to complete your masterpiece:
Painting or staining: Give your shed a fresh coat of paint or stain to protect the wood and add some personality.
Landscaping: Add some landscaping around your shed to enhance its appearance and create a welcoming space.
Building Your Dream Shed: A Real-Life Experience
Building a shed from scratch is a rewarding experience. You'll learn a lot about construction, and the end result will be a space you can truly call your own.
Remember to take your time, be patient, and don't be afraid to ask for help if you need it. And most importantly, have fun!
Bonus Tips:
Safety first: Wear safety glasses, gloves, and sturdy shoes while working.
Use quality materials: Investing in good quality lumber and other materials will ensure your shed lasts for years to come.
Don't rush: Building a shed takes time, so don't rush the process.
Document everything: Take photos and notes along the way so you can refer to them if needed.
Now get out there and start building your dream shed!
Sunday, November 10, 2024
Diy 8x12 shed plans for people who want to save money

Hey there, DIY enthusiasts! Tired of cramming all your stuff into the garage or paying an arm and a leg for a pre-built shed? You're in the right place! Building your own 8x12 shed is not only a rewarding project, but it can also save you a ton of cash.
I'm not gonna lie, it's a bit of work, but trust me, it's totally doable even if you're not a seasoned builder. We're gonna break down the whole process, step by step, so you can conquer this project with confidence.
First Things First: The Big Picture
Before you dive into the nitty-gritty, let's talk about the foundation. Your shed needs a solid base to stand on, and this is where you can already save some bucks. You have a few options:
Concrete Slab: This is the most durable choice and provides excellent stability. It's a bit more expensive upfront, but if you're planning to put a lot of weight on your shed, it's the way to go.
Concrete Piers: This is a cheaper alternative to a full slab. You'll be pouring individual piers to support the shed's corners and load-bearing walls.
Pressure-Treated Wood Skirts: This option is the most affordable but requires careful leveling and proper drainage to prevent rot.
Once you've decided on your foundation, you'll need to draw up some simple plans. There are plenty of free shed plans online, just search for "8x12 shed plans." You can also customize them to fit your specific needs.
Getting Down to Business: The Materials
Here's a basic rundown of the materials you'll need:
Lumber: Choose pressure-treated lumber for the foundation and any parts in direct contact with the ground. For the framing, you'll need a combination of 2x4s and 2x6s. Opt for quality lumber for a sturdy and long-lasting shed.
Sheathing: Plywood is a popular choice for sheathing, but OSB is a more budget-friendly option.
Roofing: Asphalt shingles are affordable and easy to install. You can also opt for metal roofing for a more durable and long-lasting option.
Doors and Windows: These are personal choices. You can buy pre-made units or build them yourself.
Hardware: Don't forget screws, nails, hinges, door handles, and any other necessary hardware.
Shop Around for the Best Deals
Now, it's time to unleash your inner bargain hunter! You can find great deals on lumber at local lumberyards or even big box stores. Check out clearance sections for potential savings on doors and windows.
The Construction Process: A Step-by-Step Guide
Alright, let's build! Here's a general outline of the process:
1. Prepare the Site: Clear the area, level the ground, and set your foundation. If you're going with concrete piers or wood skirts, make sure they're properly spaced and leveled.
2. Build the Walls: Start with the floor joists, then add the walls using the 2x4s and 2x6s. Remember to leave openings for doors and windows.
3. Add the Sheathing: Attach the plywood or OSB sheathing to the walls for added strength and stability.
4. Construct the Roof: Build the roof trusses or rafters, and attach them to the wall plates.
5. Install Roofing: Once the roof frame is complete, you can install the shingles or metal roofing.
6. Install Doors and Windows: Now it's time to hang your doors and windows, ensuring they are properly secured and weatherproofed.
7. Finish Touches: Paint or stain your shed to your liking. You can also add insulation, interior trim, and even electrical outlets if you're feeling ambitious.
Important Tips to Save Money:
Don't be Afraid to Ask for Help: You don't have to go it alone. Get friends or family involved to lend a hand and make the project more enjoyable.
Recycle and Reuse: Look for ways to reuse old materials, such as windows or doors, to save money.
Consider a Smaller Shed: If you don't need a lot of storage space, a smaller shed will require less material and be less expensive to build.
Plan Ahead: The key to saving money is to plan your project carefully. Get detailed measurements, research materials and prices, and avoid making unnecessary trips to the lumberyard.
Beyond the Basics: Adding Extra Flair
Once you've got your shed standing tall, it's time to personalize it! You can add a porch, windows, or even a loft. Let your creativity run wild!
Time for a Grand Opening!
Congratulations! You've built your own 8x12 shed and saved a ton of cash in the process. Now you can enjoy the peace of mind that comes with having a dedicated space for your belongings.
Remember, building your own shed is a rewarding experience. So, grab your tools, get your hands dirty, and get ready to enjoy the fruits of your labor. Happy building!